“There’s nothing to it but to do it”…that’s what my good friend Captain John says whenever he’s confronted with a seemingly difficult task on his RV-7 project. I don’t have any really difficult tasks brewing right now, but there are a few things in the last week that required a little braining out and that’s when I tend to overanalyze things and make them more difficult than they really are. Today’s post is an example.
There are a couple of longeron-to-firewall gussets on the forward fuse that are actually leftover parts from the RV-6. Because of that, they don’t fit precisely on the RV-7 and require some tweaking to fit.
The F-695 gussets tie together the longerons, upper firewall weldments and firewall stiffener, so they have to fit against three surfaces *and* also maintain proper 2D edge distance on the firewall and longeron rivets. As delivered the gusset doesn’t fit flush against the firewall, which would compromise edge distance on the forward rivets in the firewall stiffener. So after consulting with Vans I removed a very small amount of the gusset’s forward edge to make it fit flush.
I also had to put a slight upward bend in the forward edge (the bottom edge in this picture) to get it to lay flush on the firewall stiffener. I also laid out the rivet holes not quite per the plans; because the gusset is a few 32nds shorter, the fore-aft rivet spacing had to be adjusted a little.
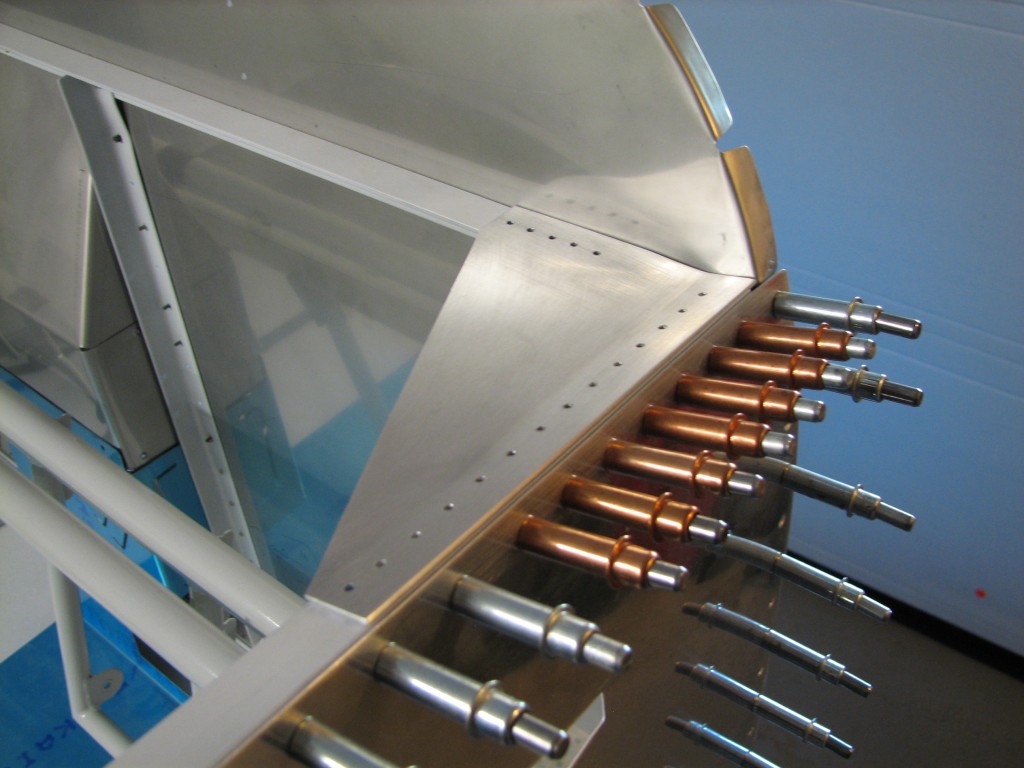
I pilot-drilled the holes to #40, clamped the gussets in place, then enlarged the holes to #30.
And they’re done, nothing left but to debur, prime and rivet. See what I mean about the overanalyzing comment?
The only downside to all this effort is that I made a big freakin’ mess in the forward floor…
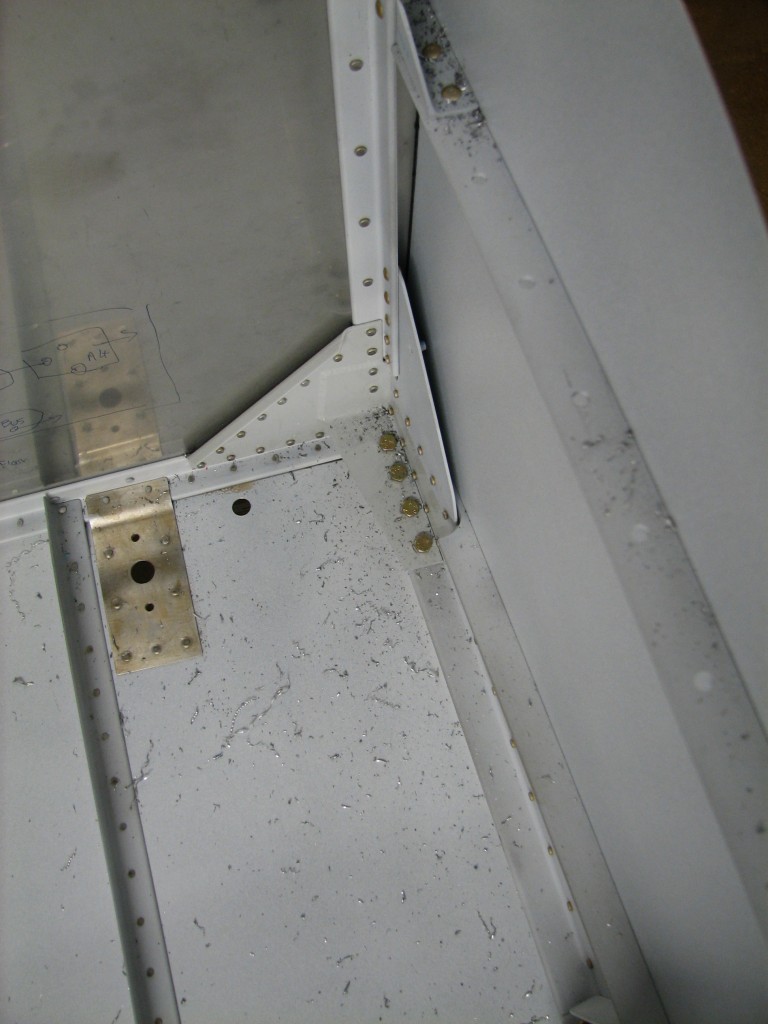
I’ve pretty much committed to installing Garmin’s G3X EFIS system as my primary flight instrumentation. Trying to get ahead of the avionics installation game, I bought a mounting bracket for the G3X magnetometer – basically an electronic compass – so I could install the bracket on the aft deck before riveting it in place. Garmin makes this bracket specifically for the RV-7/9 and has excellent instructions for aligning and installing it.
The bracket is easy to install – only six rivets – but it’s important to get it aligned closely with the aircraft centerline, otherwise the compass will have a built-in heading error. So I laid out a very precise centerline on the aft deck, clamped the mounting bracket in place against the forward flange, and match-drilled it…very easy.
There’s nothing left to do but debur, prime and rivet all the bits-and-pieces parts I’ve fitted over the last couple of weeks. I hope the Boston weather cooperates with priming…